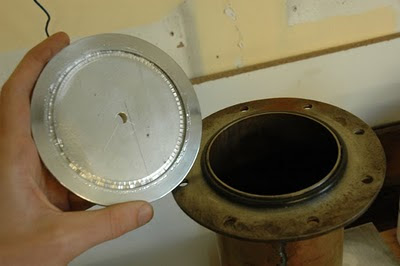
This is my blanking cap for the top of the pump barrel. Its only 6mm thick. That is the thickest I had unfortunately. I cut a groove on the lathe. As you can see it chattered a bit. Its not a big deal because it not the mating surface.
I polished the outside ring where the o-ring would press against. That all worked out well.

You see, the piece of Al. was not big enough to be a flange too, so I used this piece of acrylic as a clamp. The real problem is that the acrylic bend when you start getting near the right compression on the o-ring (20%). This, I found was deforming the cap slightly. Enough to pop the J B Welded brass adapter off.
It held long enough to do the first few tests. I am doing them at 4 Bar.
Initially I had two small leaks. So I fixed them with great enthusiasm and retested. I then found I had four leaks...
This pattern went on for two days till I finally had it sealed. So now I believe my pump is air tight. Vacuum tight? We'll see.
